Pod pojęciem trwałości konstrukcji żelbetowych rozumieć należy zdolność konstrukcji do zapewnienia właściwości użytkowych w okresie użytkowania przy minimalizacji kosztów jej utrzymania. Oznacza to, że już na etapie projektowania konieczne jest zaprojektowanie obiektu i ewentualnie środków ochrony (ochrona konstrukcyjna, materiałowo-strukturalna lub powierzchniowa), pozwalające na długotrwałą i bezproblemową eksploatację.
Przez ochronę konstrukcyjną rozumieć należy odpowiednie ukształtowanie konstrukcji, zmniejszające agresywne oddziaływanie środowiska. Ochrona materiałowo-strukturalna to odpowiedni dobór składu i struktury materiałów zwiększający odporność na agresywne środowisko eksploatacji. Ochrona powierzchniowa to ograniczenie lub odcięcie dostępu agresywnego środowiska do konstrukcji.
Korozja betonu to pogorszenie właściwości użytkowych oraz uszkodzenia konstrukcji na skutek oddziaływania środowiska. Do najważniejszych oddziaływań powodujących uszkodzenia betonu zaliczyć tu należy:
- Czynniki mechaniczne: uderzenia, przemieszczenia, drgania itp.
- Czynniki chemiczne: oddziaływania agresywnych czynników (wody gruntowe, ścieki, środki chemiczne)
- Czynniki fizyczne (cykle zamarzania i odmarzania, obciążenia termiczne – np. ogień)
- Czynniki biologiczne (grzyby, bakterie, glony, mchy)
Przykłady uszkodzeń konstrukcji żelbetowych pokazano na zdjęciach 1 i 2
Natomiast z praktycznego punktu widzenia uszkodzenia podzielić można na:
- powierzchniowe (ubytki, rysy, utrata szczelności, skażenie, zobojętnienie i odspojenie otuliny, korozja zbrojenia)
- strukturalne (pęknięcia, ugięcia, skażenie, zobojętnienie, utrata szczelności, korozja zbrojenia)
Niezależnie od przyczyn powstawania uszkodzeń konstrukcji, algorytm naprawy można przedstawić w sposób następujący:

Schemat naprawy elementu żelbetowego pokazano na rysunku nr 1 (wg [3]), ogólne zestawienie rodzajów materiałów naprawczych pokazano na rysunku nr 2 (wg [3]).
Są to materiały przeznaczone do:
- powierzchniowej ochrony konstrukcji (ograniczenie wnikania wilgoci i/lub szkodliwych czynników biologicznych i chemicznych, poprawiają trwałość konstrukcji)
- niekonstrukcyjnych napraw elementów (naprawy powierzchniowe, wypełnienie ubytków, reprofilacja elementów, przywrócenie kształtu i/lub wyglądu)
- konstrukcyjnych napraw elementów (ingerują zasadniczo w statykę konstrukcji – iniekcje scalajace i wypełnienia rys, wymiana zbrojenia,itp., prace te przywracają integralność konstrukcji i zdolność przenoszenia przez nią obciążeń).
- wzmacniania konstrukcji (zwiększenia jej nośności)
- zwiększeniu odporności na agresję chemiczną i oddziaływania fizyczne
Do najczęściej podejmowanych działań naprawczych zaliczyć można następujące operacje technologiczne:
- wypełnienie rys występujących w konstrukcji (iniekcje scalające, elastyczne wypełnienie)
- powierzchniowe wzmocnienie (impregnacja)
- ręczną reprofilację ubytków
- reprofilację ubytków poprzez nakładanie mechaniczne (torkretowanie)
- ochronę powierzchniową przez impregnację/powłoki malarskie/powłoki grubowarstwowe
Do tego może dochodzić konieczność przywrócenia ochrony zbrojenia.
Jak istotnym i skomplikowanym zagadnieniem jest naprawa i ochrona konstrukcji betonowych i żelbetowych świadczy fakt, że tylko temu zagadnieniu poświęcono 10 norm z serii PN-EN 1504 oraz ponad 65 norm dotyczących metod badań materiałów stosowanych w tych systemach.
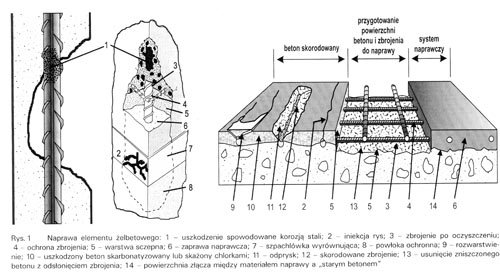
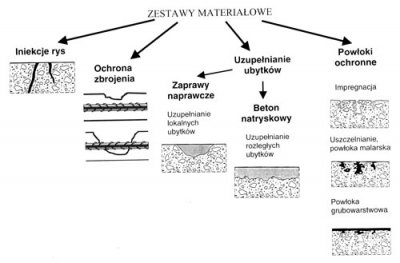
REPROFILACJA KONSTRUKCJI ŻELBETOWYCH I BETONOWYCH
Jako że wymogiem prac reprofilacyjnych jest zapewnienie trwałej i skutecznej naprawy, w skład systemów naprawczych muszą wchodzić materiały pozwalające na odpowiednio mocne zespolenie materiału naprawczego z podłożem oraz wypełnienie ubytków. Jest to:
· zaprawa do zabezpieczenia zbrojenia przed korozją
· zaprawa tworząca warstwę sczepną (w nowszych systemach zaprawa do wykonywania warstwy szcepnej i zabezpieczenia antykorozyjnego zbrojenia może być tym samym materiałem)
· zaprawa naprawcza do wypełniania ubytków
· zaprawa wyrównująco – wygłądzająca (opcjonalnie)
· warstwa ochronna ograniczająca lub odcinająca konstrukcję od wpływu agresywnego środowiska.
Taki skład systemu ma swoje uzasadnienie. Pamiętać należy, że na zdolność współpracy materiału naprawczego z podłożem ma min. wpływ:
· przyczepność zaprawy naprawczej do podłoża
· parametry wytrzymałościowe zaprawy naprawczej : wytrzymałość na ściskanie, zginanie, rozciąganie przy zginaniu
· skurcz wiązania i twardnienia
· moduł sprężystości
· współczynnik rozszerzalności termicznej
· przepuszczalność pary wodnej
· mrozoodporność, odporność na zmiany temperatury.
· odporność na agresywne czynniki znajdujące się w środowisku.
a materiał naprawczy po związaniu będzie współuczestniczył w przenoszeniu obciążeń i odkształceń konstrukcji. Dlatego też skuteczna naprawa wymaga to zastosowania materiału kompatybilnego z podłożem pod względem cech:
- fizykomechanicznych (skurcz, wytrzymałości mechaniczne, rozszerzalność termiczna itp.)
- chemicznych, elektrochemicznych (możliwość powstawania mikroogniw korozji wkładek zbrojeniowych)
- szczelnościowych (odspojenie się zbyt szczelnej zaprawy naprawczej na skutek dyfuzji pary wodnej).
Do napraw konstrukcji mogą być stosowane:
- zaprawy i betony hydrauliczne (CC) -wykonane przez zmieszanie spoiwa hydraulicznego z kruszywem, twardniejące w wyniku reakcji hydratacji po zmieszaniu z wodą, mogące zawierać domieszki i dodatki.
- zaprawy i betony polimerowo-cementowe (PCC) – zaprawy/betony hydrauliczne modyfikowane przez dodanie polimeru. Stosowane polimery obejmują głównie:
– żywice akrylowe, metakrylowe lub modyfikowane akrylowe w postaci rozpuszczalnych proszków lub dyspersji wodnych
– polimery, kopolimery i terpolimery winylowe w postaci rozpuszczalnych proszków lub dyspersji wodnych;
– kauczuk styrenowo-butadienowy tylko w postaci dyspersji wodnych;
– naturalne lateksy kauczukowe;
– epoksydy.
- zaprawy i betony polimerowe (PC) – mieszanki spoiw polimerowych i kruszywa utwardzające się w reakcji polimeryzacji
Najczęściej do napraw stosuje się zaprawy PCC i SPCC (polimerowo-cementowe zaprawy naprawcze do nakładania, odpowiednio: ręcznego i natryskowego).
Zaprawy PCC klasyfikuje się następująco
· PCC I – do stosowania na powierzchnie obciążone dynamicznie (w tym ruchem kołowym)
· PCC II – do stosowania na powierzchnie obciążone dynamicznie (lecz bez ruchu kołowego)
· PCC III – do stosowania na powierzchnie nie obciążone dynamicznie
Zaprawy SPCC klasyfikuje się następująco
· SPCC II – do nakładania na powierzchnie obciążone dynamicznie (lecz bez ruchu kołowego) lub w położeniu sufitowym
· SPCC III – do nakładania na powierzchnie nie obciążone dynamicznie oraz na powierzchnie pionowe i nachylone
Wymagania dla materiałów naprawczych wg PN-EN 1504-3 podano w tabelach 1 i 2.
Ostateczny dobór systemu naprawy (a więc także zdefiniowanie wymaganych właściwości) następuje na etapie opracowywania dokumentacji technicznej.
Niezbędnym warunkiem poprawności wykonywanych robót jest odpowiednie przygotowanie podłoża. Należy usunąć wszystkie luźne, osłabione korozją i skażone fragmenty aż do odsłonięcia nienaruszonego, nieskorodowanego i nieskarbonizowanego betonu. W zależności od kształtu powierzchni i stopnia zniszczenia betonu przygotowanie powierzchni może być przeprowadzone przez szczotkowanie, szlifowanie, skuwanie, piaskowanie, śrutowanie oraz metody hydrodynamiczne. Stosowanie wody pod wysokim ciśnieniem jest szybkim i skutecznym sposobem usuwania betonu, ograniczającym do minimum straty betonu nieuszkodzonego. Nie występują mikrospękania, a beton uszkodzony jest usuwany selektywnie, pozostawiając pozostały beton nienaruszony. Metodę tę można zastosować, jeśli używa się sprzętu o znanych parametrach użytkowych. Wymagania, które należy spełnić, to rozróżnienie między betonem uszkodzonym a pozostałym. Możliwe jest usunięcie betonu do wstępnie założonej głębokości, jednakże w przypadku lokalnie osłabionego betonu głębokość ta ulegnie zwiększeniu.
Właściwości użytkowe | Zasada naprawy | |||
3 | 4 | 7 | ||
Metoda naprawy | ||||
3.1, 3.2 | 3.3 a | 4.4 | 7.1 , 7.2 | |
Wytrzymałość na ściskanie | ■ | ■ | ■ | ■ |
Zawartość jonów chlorkowych b | ■ | ■ | ■ | ■ |
Przyczepność | ■ | ■ | ■ | ■ |
Ograniczony skurcz/pęcznienie c | ■ | ■ | ■ | ■ |
Trwałość a) Odporność na karbonatyzację b d |
■ | ■ | ■ | ■ |
Trwałość b) Kompatybilność cieplna EN 13687, Część 1, lub Część 2, lub Część 4 e |
○ | ○ | ○ | ○ |
Moduł sprężystości | ○ | ○ | ■ | ○ |
Odporność na poślizg f | ○ | ○ | ○ | ○ |
Współczynnik rozszerzalności cieplnej c g | ○ | ○ | ○ | ○ |
Absorpcja kapilarna (przepuszczalność wody) e h | ○ | ○ | ○ | ○ |
Zasady napraw zgodnie z ENV 1504-9:1997: Zasada 3 – odbudowanie elementu betonowego Zasada 4 – wzmacnianie konstrukcji Zasada 7 – utrzymanie lub przywrócenie stanu pasywnego Metody napraw zdefiniowane w ENV 1504-9:1997:
7.1 Zwiększenie grubości otuliny zbrojenia przez dodanie zaprawy lub betonu cementowego. 7.2 Wymiana skażonego lub skarbonatyzowanego betonu. |
||||
aZe względu na sposób nakładania, niektóre metody badań mogą być modyfikowane. Patrz EN 14487-1. b To wymaganie nie dotyczy napraw betonu niezbrojonego. c Jeśli stosowane są cykle cieplne, to badanie nie jest wymagane. d To badanie nie jest przydatne, jeśli system naprawczy zawiera system ochrony powierzchniowej o potwierdzonej zdolności ochrony przed karbonatyzacją (patrz EN 1504-2) lub stanowi zaprawę PC. e Zależnie od warunków ekspozycji środowiskowej. f Stosuje się tylko do obszarów, na których odbywa się ruch. g Stosuje się tylko do PC h Odporności korozyjnej dotyczą wymagania odnośnie do zawartości chlorków i przepuszczalności wody. |
W stosowanych zazwyczaj urządzeniach do usuwania betonu strumieniem wody pod ciśnieniem wykorzystuje się ciśnienie 60-110 MPa. W przypadku selektywnego usuwania betonu tą metodą konieczne jest uprzednie określenie w SST odpowiedniego sprzętu. Szorstkość powierzchni może się znacząco różnić w zależności od odległości między dyszą a podłożem, ciśnienia wody, strumienia wody, szybkości podawania wody, stosowanego sprzętu oraz jakości betonu.
Ciśnienie wody, mierzone zazwyczaj na pompie, może być kategoryzowane następująco:
– niskie ciśnienie do 18 MPa – stosowane do oczyszczania podłoża betonowego. Ciśnienie > 8 MPa pozwala także na usunięcie zmurszałych i niestabilnych fragmentów podłoża
– wysokie ciśnienie od 18 MPa do 60 MPa – stosowane do usuwania skorodowanych i niestabilnych warstw betonu o większej grubości.
- bardzo wysokie ciśnienie od 60 MPa – stosowane do usuwania betonu, jeśli konieczne jest ograniczenie ilości używanej wody.
Pamiętać należy, że usuwanie niestabilnego betonu powinno być ograniczone do minimum, nie powinno ono zmniejszać strukturalnej integralności konstrukcji w sposób uniemożliwiający spełnianie przez nią założonych funkcji. Krawędzie w miejscach usuwania betonu powinny być przycięte pod kątem nie mniejszym niż 90°, aby uniknąć podcięcia, i nie większym niż 135°, aby zmniejszyć możliwość odspojenia wraz z warstwą wierzchnią przyległego, nieuszkodzonego betonu. Powierzchnia krawędzi powinny być uszorstnione w stopniu wystarczającym do zapewnienia przyczepności pomiędzy materiałem oryginalnym a naprawczym. Jeżeli na powierzchni pręta zbrojeniowego, odsłoniętej po usunięciu uszkodzonego betonu, występuje korozja, konieczne może być zwiększenie głębokości usuwania betonu w celu odsłonięcia całego pręta. Zaleca się, aby prześwit wokół zbrojenia i minimalna odległość między prętem zbrojeniowym a pozostałym podłożem wynosił co najmniej 15 mm lub odpowiadał maksymalnemu wymiarowi ziarna kruszywa materiału naprawczego powiększonemu o 5 mm, zależnie od tego, która z tych wartości jest większa.
![]() Fot. 1
|
![]() Fot 2.
|
Niezależnie od zastosowanej metody usuwania niezwiązanych cząstek betonu zawsze konieczne jest oczyszczenie z rdzy istniejącego zbrojenia. Zbrojenie może być oczyszczane np. odbijakami igłowymi, wodą pod ciśnieniem 20-70 MPa, metodą hydropiaskowania, strumieniowania ściernego czy też poprzez szczotkowanie drucianymi szczotkami (w tym ostatnim przypadku zalecanym sposobem jest mechaniczne szczotkowanie. Szczotkowanie jest mało efektywne przy oczyszczaniu zbrojenia od strony skutego podłoża betonowego, przy całkowitym odsłonięciu pręta po obwodzie). Uszkodzone lub zbyt skorodowane pręty mogą wymagać wymiany.
Ostatecznie podłoże podłoże pod prace reprofilacyjne musi być czyste, stabilne, zdrowe, szorstkie i otwartoporowe. Następnym etapem robót jest nawilżenie podłoża do stanu matowo-wilgotnego. Pierwsze nasycenie należy przeprowadzić kilka-kilkanaście godzin przed rozpoczęciem robót przez spryskiwanie powierzchni wodą aż do uzyskania stanu matowo-wilgotnego (Za podłoże matowo-wilgotne uważa się beton o jednorodnej, ciemnej i matowej powierzchni. Woda naniesiona na tak przygotowane podłoże musi w krótkim czasie ulec wchłonięciu, nie może występować na powierzchni błyszcząca warstewka wody). W razie potrzeby krótko przed rozpoczęciem robót zabieg powtórzyć usuwając nadmiar wody np. sprężonym powietrzem. Proces wysycania podłoża umożliwia uzyskanie odpowiedniej przyczepności warstwy naprawczej do podłoża. Zbyt suche podłoże wchłonie z warstwy sczepnej wilgoć niezbedną dla prawidłowego przebiegu procesu hydratacji. Warstwę sczepną nanosi się zawsze wcierając zaprawę twardym pędzlem lub szczotką w podłoże. Pozwala to na dokładne wypełnienie porów podłoża zaprawą (porównaj rysunek 3).
Kolejną fazą robót jest powleczenie odkrytego zbrojenia preparatem antykorozyjnym oraz zagruntowanie całej powierzchni ubytku preparatem tworzącym tzw. warstwę sczepną. Tworzy ona rodzaj membrany pomiędzy starym betonem oraz materiałem, z którego została wykonana naprawa. Jej zwiększona podatność uniemożliwia powstawanie zbyt dużych naprężeń w strefie styku powstałych na skutek różnic w zakresie odkształceń sprężystych, termicznych czy też powstałych na skutek obciążenia odrywającego. Brak warstwy sczepnej może doprowadzić do zarysowania i naderwania warstwy renowacyjnej (w systemach nakładanych mechanicznie warstwa sczepna nie występuje).
Kolejnym etapem jest, w zależności od charakteru usuwanych uszkodzeń nałożenie właściwej masy naprawczej. Głębokość ubytków może być bardzo różna, od kilku milimetrów do kilkunastu nawet centymetrów. Nie jest możliwa reprofilacja podłoża w tak szerokim zakresie głębokości przy pomocy jednej, uniwersalnej zaprawy naprawczej. Oznacza to, że w systemie znajduje się zazwyczaj kilka zapraw naprawczych, stosowanych przy różnych głębokościach ubytków. Dodatkowo, reprofilacja ubytków o głębokości rzędu 3 cm i większych nie może następować w jednej warstwie. Taką zaprawę nakłada się w kilku warstwach, pierwszą warstwę zawsze na warstwę sczepną, kolejne warstwy natomiast można nakładać w kilkugodzinnych zazwyczaj odstępach, już bez warstwy sczepnej między poszczególnymi warstwami tej samej zaprawy naprawczej. Należy tu jednakże zwrócić uwagę na rzecz następującą. Odstęp między kolejnymi cyklami roboczymi nie może być dłuższy niż podany w karcie technicznej konkretnej masy PCC. W przeciwnym razie konieczne jest dodatkowe wykonanie warstwy sczepnej.
Stosowanie szpachli wygładzającej nie jest obligatoryjne, jednak przy reprofilacji głębszych ubytków (rzędu 5 cm i większych) stosowana zaprawa naprawcza zawiera gruboziarniste kruszywo, szpachlowanie wygładzające jest w zasadzie niezbędne pod wymalowania czy powłoki ochronne. Nakładanie szpachli wygładzającej wykonywane jest zasadniczo w dwóch przejściach. W pierwszym przejściu w odpowiednio przygotowane podłoże wciera się twardą szczotka lub pędzlem pierwszą warstwę szpachli, i natychmiast potem nakłada się pacą zaprawę naprawczą w jednym przejściu na żądaną grubość.
W przypadku napraw dużych powierzchni korzystne jest stosowanie zapraw SPCC (polimerowo-cementowe zaprawy do nakładania mechanicznego). Prace polegają na mechanicznym natryśnięciu zaprawy naprawczej na wcześniej przygotowane i oczyszczone podłoże. Stosuje się dwie metody natrysku:
- metoda sucha – polega na osobnym doprowadzeniu do dyszy suchej zaprawy oraz wody, zatem połączenie się tych składników następuje w samej dyszy oraz na odcinku od dyszy do podłoża.
- metoda mokra – zarobiona wodą zaprawa dostarczana jest przy pomocy pompy do dyszy, skąd pneumatycznie jest natryskiwana na podłoże.
Metoda mokra cechuje się lepszą jednorodnością natryskiwanej zaprawy, mniejszymi stratami odbicia jak również mniejszym zapyleniem podczas wykonywania robót. Metoda sucha pozwala na korektę konsystencji mieszanki w chwili nakładania (istotne przy wykonywaniu prac w położeniu sufitowym) i daje lepsze zagęszczenie nałożonego materiału przy mniejszym niż w metodzie mokrej stosunku w/c.
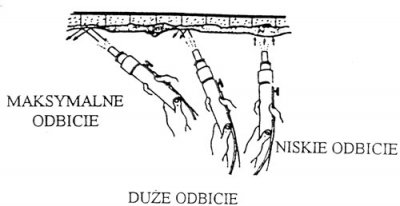
Na prawidłową aplikację ma przede wszystkim wpływ dobór typu dyszy i jej średnicy, ciśnienie natrysku, odpowiednia średnica i długość węży agregatu natryskowego, warunki atmosferyczne (wilgoć, wiatr, temperatura), konsystencja natryskiwanego materiału oraz odpowiednie przygotowanie podłoża (oczyszczenie, nawilżenie, szorstkość – w metodzie natryskowej nie stosuje się warstwy sczepnej).
Na wielkość strat odbicia największy wpływ ma sposób nakładania zapraw naprawczych (patrz rysunki 4 wg [2]). Szczególną uwagę należy zwracać na obecność zbrojenia, które musi zostać poprawnie „otulone” zaprawą naprawczą, przykład niepoprawnego i poprawnego natrysku pokazano na rysunku 5 (wg [2])
Dokumentacja techniczna prac naprawczych powinna zawierać przede wszystkim informacje o:
- rodzaju zastosowanych materiałów naprawczych
- badaniach stanu powierzchni przed rozpoczęciem robót
- warunkach cieplno-wilgotnościowych podczas aplikacji i pielęgnacji materiałów reprofilacyjnych oraz sposobach ich określania (jeżeli to wymagane)
- badaniach kontrolnych na poszczególnych etapach prac reprofilacyjnych.
Kontrola poprawności wykonanych prac na każdym ich etapie jest obowiązkiem zarówno wykonawcy jak i nadzoru inwestorskiego. Wymusza to więc na wykonawcy zatrudnianie wykfalifikowanego personelu oraz posiadanie odpowiedniego sprzętu do przygotowania powierzchni (urządzenia hydrodynamiczne, strumieniowo-ścierne, młoty, piły itp.). Dla poprawnego określenia warunków aplikacji niezbędne może być posiadanie termometrów do określenia temperatury podłoża i powietrza, wilgotnościomierzy do pomiaru wilgotności powietrza i podłoża, przyrządy do pomiaru przyczepności („pull-off”) oraz urządzeń do pomiaru grubości nałożonych powłok (w stanie mokrym i po związaniu). Woda zarobowa musi być wodą czystą, najlepiej wodociągową lub pitną, niedopuszczalne jest stosowanie wody pochodzącej z niewiadomego źródła.
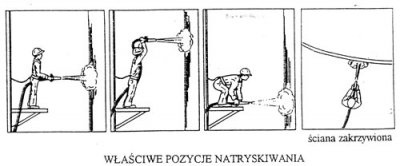
W wątpliwych przypadkach korzystne jest wykonanie napraw próbnych i ocena ich skuteczności. Należy także na bieżąco przeprowadzać niezbędne badania kontrolne na pośrednich etapach prac reprofilacyjnych oraz rejestrować warunki atmosferyczne.
Bardzo istotna jest odpowiednia pielęgnacja nałożonej naprawy. Musi ona polegać na utrzymywaniu zaprawy w odpowiedniej wilgotności (poprzez zraszanie wodą) przynajmniej przez kilka dni po nałożeniu (szczegółowe wytyczne dotyczące sposobu aplikacji, grubości nakładanych warstw czy sposobu pielęgnacji znajdują się zawsze w kartach technicznych stosowanych zapraw naprawczo-reprofilacyjnych).
Naprawa/uszczelnienie przez iniekcję
Norma PN-EN 1504-5:2006 Wyroby i systemy do ochrony i napraw konstrukcji betonowych. Definicje, wymagania, sterowanie jakością i ocena zgodności. Część 5: Iniekcja betonu dzieli wyroby iniekcyjne na trzy kategorie:
- wyroby iniekcyjne do przenoszącego siły wypełniania rys, pustek i szczelin w betonie (F) są to wyroby, które mogą tworzyć połączenie z powierzchnią betonu i przenosić siły
- wyroby iniekcyjne do elastycznego wypełniania rys, pustek i szczelin w betonie (D) są to elastyczne wyroby, które mogą dostosowywać się do kolejnych odkształceń
- wyroby iniekcyjne dopasowujące się przez pęcznienie do wypełniania rys, pustek i szczelin w betonie (S) są to wyroby, które w stanie utwardzonym mogą wielokrotnie pęcznieć na skutek adsorpcji wody, przy czym woda jest wiązana przez składnik wyrobu iniekcyjnego
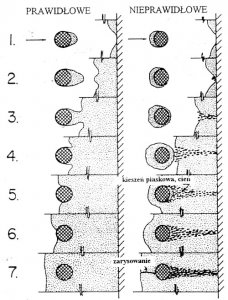
Norma ta nie obejmuje natomiast wstępnych prac iniekcyjnych, jeśli są konieczne, prowadzonych w celu czasowego powstrzymania wypływu wody w czasie iniekcji uszczelniającej.
Do wykonywania iniekcji stosuje się:
- iniekty epoksydowe – są to dwuskładnikowe preparaty stosowane do siłowego sklejania rys suchych lub (rzadziej) lekko wilgotnych, o ustabilizowanej szerokości rozwarcia (zmiana szerokości rozwarcia nie powinna przekraczać 0,03mm). W składzie zawierają niskocząsteczkowy roztwór żywicy epoksydowej oraz utwardzacz. Ze względu na niewielką elastyczność i wysokie parametry wytrzymałościowe bezkrytyczne stosowanie epoksydów do iniekcji może doprowadzić do miejscowego przesztywnienia iniekowanego elementu
- iniekty poliuretanowe – stosowane są do iniekcji i uszczelnień rys wilgotnych i mokrych oraz przewodzących wodę. Elastyczność poliuretanów po związaniu powoduje że są chętnie stosowane także w przypadku rys o nieustabilizowanej szerokości rozwarcia. W zależności od składników i modyfikatorów cechują się różnymi właściwościami. Jednoskładnikowe (zawierają modyfikowane izocyjaniany i katalizatory) silnie pienią się w kontakcie z wilgocią i są stosowane do tamowania wycieków wody. Dwuskładnikowe, na bazie polieteropolioli i izocyjanianów, o mniejszej podatności do spieniania się najczęściej stosowane są do iniekcji wtórnych – doszczelniajacych jak również do wypełniania rys suchych i zawilgoconych. Ze względu na elastyczność po związaniu bardzo chętnie stosowane są do uszczelnień rys o zmiennej szerokości rozwarcia oraz do napraw konstrukcji murowych.
- iniekty poliakryloamidowe – cechują się zdolnością do pęcznienia w kontakcie z wodą. Reakcja polimeryzacji zaczyna się po dodaniu inicjatora i przyspieszacza (dlatego istnieje tu możliwość dobierania czasu wiązania). Są stosowane do uszczelniania wilgotnych i mokrych rys w konstrukcjach żelbetowych i murach. Dobrze zwilżają podłoże betonowe i mają niską lepkość (w stanie nieutwardzonym).
- iniekty akrylowe – (na bazie polimetakrylanu metylu) wykazują bardzo dobrą przyczepność do podłoży betonowych. Ze względu na niską lepkość i zdolność do penetracji mikrorys stosowane są do napraw konstrukcji betonowych w niskich temperaturach. Można w nich regulować szybkość reakcji
- iniekty cementowe oraz mikrocementowe – pozwalają na iniekcję rys o szerokości rozwarcia odpowiednio od 2mm i od 0,1mm. Kolejną odmianą iniektów cementowych są iniekty polimerowo-cementowe, będące zazwyczaj dwuskładnikowymi preparatami zawierającymi cement, modyfikatory, wypełniacze oraz płynne roztwory kopolimerów akrylu lub emulsje butadienowo-styrenowe. W porównaniu do typowych iniektów cementowych obecność tworzyw sztucznych (polimerów) zwiększa przyczepność do ścianek rysy oraz zwiększa elastyczność związanego iniektu. Jednoskładnikowe iniekty polimerowo-cementowe zawierają w składzie redyspergowalne tworzywa sztuczne, dlatego mieszane są tylko z wodą.
Dla iniektów epoksydowych i poliuretanowych za minimalną temperaturę aplikacji przyjmuje się + 100C, choć wiązanie żywic możliwe jest już w temperaturze + 50C, jednakże ze względu na znaczne pogorszenie zdolności penetracji w tym zakresie temperatury, skuteczna iniekcja może być trudna do przeprowadzenia. Iniekty na bazie cementów, polimerocementów czy żywic poliakrylamidowych wymagają temperatury przynajmniej + 50C.
Iniekty epoksydowe są z reguły wrażliwe na obecność wilgoci/wody w rysie. Zaburza ona proces wiązania żywicy.
W przypadku iniekcji zaczynami cementowymi może dojść do odciągnięcia przez beton wody niezbędnej do procesu hydratacji zaczynu cementowego, dlatego korzystne tu może być nawilżenie suchych rys przed iniekcją. Iniekcja w mokrą rysę przy źle dobranych parametrach procesu może powodować, że woda obecna w rysie lokalnie zawyża proporcji woda-cement w iniekcie, co prowadzi do pogorszenia jego parametrów. Iniekty mikrocementowe są ponadto wrażliwe na sposób mieszania. Cechą mikrocementów jest zdolność do penetracji w rysy o niewielkiej szerokości rozwarcia. Nieodpowiednie zarobienie preparatu np. za pomocą tradycyjnego mieszadła może doprowadzić do powstania skupisk ziaren cementu uniemożliwiających właściwą penetrację zaczynu w rysy.
Nr | Właściwość użytkowa | Podłoże kontrolne (EN 1766) | Metoda badania | Wymaganie | |||
Naprawa | konstrukcyjna | Naprawa niekonstrukcyjna | |||||
Klasa R4 | Klasa R3 | Klasa R2 | Klasa R1 | ||||
1 | Wytrzymałość na ściskanie | Brak | EN 12190 | ≥ 45 MPa | ≥ 25 MPa | ≥ 15 MPa | ≥ 10 MPa |
2 | Zawartość jonów chlorkowych | Brak | EN 1015-17 | ≤ 0,05 % | ≤ 0,05 % | ||
3 | Przyczepność | MC(0,40) | EN 1542 | ≥ 2,0 MPa | ≥ 1,5 MPa | ≥ 0,8 | MPa a |
4 | Ograniczony skurcz/pęcznienie bc | MC(0,40) | EN 12617-4 | Przyczepność po badaniu d e | Brak wymagań | ||
≥ 2,0 MPa | ≥ 1,5 MPa | ≥ 0,8 MPa a | |||||
5 | Odporność na karbonaty-zację ‘ | Brak | EN 13295 | dk < betonu kontrolnego (MC(0,45)) | Brak wymagań g | ||
6 | Moduł sprężystości | Brak | EN 13412 | ≥ 20 GPa | ≥ 15 GPa | Brak wymagań | |
7 | Kompatybilność cieplna f h Część 1, Zamrażanie-roz-mrażanie | MC(0,40) | EN 13687-1 | Przyczepność po 50 cyklach d e | Sprawdzenie wizualne po 50 cyklach e | ||
≥ 2,0 MPa | ≥ 1,5 MPa | ≥ 0,8 MPa | |||||
8 | Kompatybilność cieplna f h Część 2, Zraszanie | MC(0,40) | EN 13687-2 | Przyczepność po 30 cyklach d e | Sprawdzenie wizualne po 30 cyklach e | ||
≥ 2,0 MPa | ≥ 1,5 MPa | ≥ 0,8 MPa a | |||||
9 | Kompatybilność cieplna f h Część 4, Cykle suszenia | MC(0,40) | EN 13687-4 | Przyczepność po 30 cyklach d e | Sprawdzenie wizualne po 30 cyklach e | ||
≥ 2,0 MPa | ≥ 1,5 MPa | ≥ 0,8 MPa a | |||||
10 | Odporność na poślizg | Brak | EN 13036-4 | Klasa l: > 40 jednostek przy badaniu na mokro Klasa II: > 40 jednostek przy badaniu na sucho Klasa III: > 55 jednostek przy badaniu na mokro |
Klasa l: > 40 jednostek przy badaniu na mokro Klasa II: > 40 jednostek przy badaniu na sucho Klasa III: > 55 jednostek przy badaniu na mokro |
||
11 | Współczynnik rozszerzalności cieplnej c | Brak | EN 1770 | Nie wymagane, jeśli przeprowadza się badanie 7, 8 lub 9, w innym przypadku wartość deklarowana | Nie wymagane, jeśli przeprowadza się badanie 7, 8 lub 9, w innym przypadku wartość deklarowana | ||
12 | Absorpcja kapilarna | Brak | EN 13057 | ≤ 0,5 kg*m-2*h-0,5 |
≤ 0,5 kg*m-2*h-0,5 |
Brak wymagań | |
a Osiągnięcie wartości 0,8 MPa nie jest wymagane, jeśli następuje zniszczenie kohezyjne w materiale naprawczym. W takim przypadku wymagana jest minimalna wytrzymałość na rozciąganie 0,5 MPa. b Nie wymagane przy metodzie 3.3. c Nie wymagane, jeśli stosuje się cykle cieplne. d Wartość średnia przy braku pojedynczych wartości mniejszych niż 75 % wymaganego minimum. e Maksymalna dopuszczalna średnia szerokość rysy ≤ 0,05 mm przy braku rys ≥0,1 mm i braku odspojeń. f Dla trwałości. g Nie stosuje się przy ochronie przed karbonatyzacją, chyba że system naprawczy zawiera system ochrony powierzchniowej o potwierdzonej zdolności ochrony przed karbonatyzacją (patrz EN 1504-2). h Wybór metody zależy od warunków ekspozycji. Jeśli wyrób spełnia wymagania Części 1, uznaje się, że spełnia także wymagania Części 2 i Części 4. |
Podstawowe wymagania stawiane przez normę PN-EN 1504-5:2006 materiałom do wykonywania iniekcji podano w tabelach 3-5.
Iniekcja jest jednym z najtrudniejszych etapów naprawy konstrukcji betonowych i żelbetowych. Wynika to z faktu, że na skuteczność naprawy ma wpływ wiele czynników, w tym nie wszystkie są w momencie wykonywania prac „mierzalne”. Czynnikiem determinującym dobór materiału iniekcyjnego jest cel iniekcji i warunki jego przeprowadzania (patrz tabela 6)
Do podstawowych czynności wykonywanych przed rozpoczęciem prac iniekcyjnych zaliczyć trzeba:
- określenie stanu przegrody i materiału użytego do jej wykonania
- określenie warunków użytkowania obiektu.
- określenie typu rysy: powierzchniowa, konstrukcyjna
- określenie przebiegu rys
- określenie szerokości rozwarcia rys
- określenie zmian szerokości rozwarcia rys
- określenie wilgotności rysy – rysa sucha, wilgotna/mokra, przeciekająca (rysa sucha – brak wody w rysie lub na jej ściankach; wykluczone jest przemieszczanie się wody w rysie w czasie iniekcji i utwardzania wyrobu iniekcyjnego, rysa wilgotna – brak wody w rysie, obecność wody na ściankach bocznych rysy, jednakże bez warstwy wody na powierzchni ścianek, rysa mokra – charakterystyczna dla mokrej rysy jest obecność kropel wody na powierzchni rysy, rysa przeciekająca – woda płynąca przez rysę) oraz określenie jej zanieczyszczeń
Na tej podstawie dobiera się odpowiedni środek iniekcyjny, określa rodzaj i sposób osadzenia i rozmieszczenia końcówek iniekcyjnych (naklejane, wbijane, osadzane w nawierconych otworach oraz określa metodę i parametry iniekcji (czas, ciśnienie)
Iniekcje w rysy suche lub wilgotne.
Tego typu iniekcje mogą mieć na celu siłowe sklejenie elementu lub zamknięcie rysy. Wymagane jest tu zazwyczaj powierzchniowe uszczelnienie rysy. Mogą tu być stosowane pakery naklejane (rysunek 6), wbijane lub wkręcane. Odstęp między pakerami uzależniony jest od grubości naprawianego elementu, głębokości iniektowanej rysy oraz jej szerokości. Nie może on być większy niż głębokość rysy lub grubość elementu (decyduje mniejsza wielkość). Przyjmuje się ponadto, że dla rysy o szerokości rozwarcia do 0,2mm włącznie odstęp nie może być większy niż 15cm, przy szerokości rozwarcia rysy nie mniejszej niż 1mm odstęp między pakerami może wynosić nawet 50 cm. Stosowanie pakerów naklejanych wymusza powierzchniowe uszczelnienie rysy specjalnymi szpachlówkami mineralnymi lub masami epoksydowymi. Ich przyczepność do podłoża nie powinna być mniejsza niż 1,5 MPa, a grubość szpachli nie może być mniejsza niż 3 mm. Powierzchniowe uszczelnienie rysy wymagane jest w przypadku iniekcji sklejającej.
Inną metodą iniekcji jest nawiercanie otworów wzdłuż przebiegu rysy, po obu jej stronach i pod kątem 45 stopni (rysunek 7, fot. 3). Powinny one przecinać rysę w połowie jej głębokości. Zarówno w pierwszym jak i w drugim przypadku konieczne jest odessanie odwiertów i rysy przed obsadzeniem pakerów. Nie jest tu zalecane przedmuchiwanie otworów, może to spowodować zatkanie rysy.
Rozróżnia się trzy typy iniekcji:
- niskociśnieniową – do 0,15 MPa
- średniciśnieniową – od 0,18 MPa do 0,80 MPa
- wysokociśnieniową – powyżej 0,80 MPa
Przy pionowym przebiegu rysy iniekcję należy zaczynać zawsze od dołu rysy, przesuwając się w miarę wypełniania rysy do jej górnej części, niezależnie od typu stosowanych pakerów. W razie wystąpienia jakichkolwiek problemów w trakcie iniekcji korzystne może być doiniektowanie poszczególnych pakerów, przeprowadzone jeszcze przed związaniem iniektu. Dla rys poziomych iniekcję należy zaczynać zawsze od pakera skrajnego.
Iniekcje w rysy przewodzące wodę.
Przy iniekcji rys nawodnionych proces przebiega dwuetapowo. W pierwszej fazie stosuje się iniekcję silnie spieniającą się żywicą poliuretanową. Powoduje ona przede wszystkim zatrzymanie przecieku wody, jednak jej działanie nie jest trwałe, dlatego też w drugim etapie wtłacza się bardziej elastyczny, powodujący trwałe uszczelnienie iniektami, także na bazie poliuretanów. Nie cechuje się on właściwościami spieniającymi, lecz elastycznymi i to on decyduje o trwałości uszczelnienia.
Ciśnienie procesu oraz ilość wtłaczanego iniektu zależy od intensywności przecieku przez rysę, ciśnienia przecieku oraz geometrii rysy.
Podczas prac iniekcyjnych należy stale kontrolować cały proces, zwracając uwagę szczególnie na wszelkiego rodzaju utrudnienia czy przerwy oraz inne nieprawidłowości, wymagające niekiedy konieczności zmiany rodzaju iniektu czy parametrów procesu. Będą to przede wszystkim: nieadekwatna do rozmiarów rysy ilość wtłaczanego iniektu oraz brak ciągłości przy wypełnianiu rysy zaobserwowany na sąsiadujących pakerach. Całość prac iniekcyjnych należy ponadto odpowiednio udokumentować, rejestrując rozmieszczenie pakerów w stosunku do przebiegu rysy, stan wilgotnościowy iniekowanej przegrody, warunki cieplno-wilgotnościowe występujące podczas procesu, ciśnienia robocze (początkowe i końcowe), ilość zużytego iniektu oraz uwagi o zakłóceniach i przeszkodach wynikłych w trakcie robót.
Literatura
[1] – W. Kiernożycki „Betonowe konstrukcje masywne”, Polski Cement 2003
[2] – G.Słowek, W. Majchrzak „Naprawy konstrukcji żelbetowych metodą torkretowania”, XIII Ogólnopolska konferencja Warsztat Pracy Projektanta, Ustroń 1998, Materiały konferencyjne.
[3] – L. Czarnecki, P.H. Emmons – „Naprawa i ochrona konstrukcji betonowych”, Polski Cement, Kraków 2002
[4] – L. Czarnecki – „Materiały do napraw i wzmocnień konstrukcji żelbetowych” XIII Ogólnopolska konferencja Warsztat Pracy Projektanta, Ustroń 1998, Materiały konferencyjne.
[5] – L. Czarnecki, J. Skwara – „ Naprawa rys konstrukcji żelbetowych metodą iniekcji” XIII Ogólnopolska konferencja Warsztat Pracy Projektanta, Ustroń 1998, Materiały konferencyjne.
[6] – W.Kiernozycki, A.Adamczyk – „ Naprawa i uszczelnianie dylatacji w konstrukcjach żelbetowych” XIII Ogólnopolska konferencja Warsztat Pracy Projektanta, Ustroń 1998, Materiały konferencyjne.
[7] – M. Rokiel – „Naprawa dylatacji w konstrukcjach żelbetowych materiałami firmy Schomburg”. Materiały konferencyjne z Seminarium Naukowo-Technicznego: Materiały firmy Schomburg stosowane do uszczelnień betonów w konstrukcjach hydrotechnicznych. Akademia Rolnicza w Poznaniu. VI.2004
[8] – G. Wischers, J. Dahms – „Das Verhalten des Betons bei sehr niedrigen Temperaturen“ Beton 4, 1970
[8] – R. Lindner – „Baukoerpers aus wasserundurchlaessigem Beton“ Beton-Kalender, Berlin 1986
[10] – J. Kobiak, W. Stachurski – „Konstrukcje żelbetowe”, t 4, Arkady 1991
[11] – L. Czarnecki, J. Skwara – „Naprawa konstrukcji murowych przez iniekcję”, XIV Ogólnopolska Konferencja: Warsztat pracy projektanta konstrukcji, PZiTB Bielsko Biała 1999
[12] – DafSTb Richtlinie – Wasserundurchlässige Bauwerke aus Beton (WU-Rich-tlinien) ,Entwurf II.2002
[13] – K. Flaga – „Zbrojenie przeciwskurczowe, obliczenia, zalecenia konstrukcyjne w budownictwie powszechnym.” Warsztat Pracy Projektanta Konstrukcji, Ustroń 2002
[14] – Z. Ściślewski – „Trwałość konstrukcji żelbetowych” ITB 1995
[15] – J. Pasławski, M.Gajzler – „Systemowy dobór materiału do napraw konstrukcji betonowych” , XII Konferencja naukowo techniczna OKTRA 2001, Materiały konferencyjne
[16] – Maciej Rokiel – Poradnik Hydroizolacje w budownictwie. Wybrane zagadnienia w praktyce. Dom Wydawniczy MEDIUM, Warszawa 2006
[17] – PN-EN 1504-1:2006 Wyroby i systemy do ochrony i napraw konstrukcji betonowych – Definicje, wymagania, kontrola jakości i ocena zgodności – Definicje
[18] – PN-EN 1504-2:2006 Wyroby i systemy do ochrony i napraw konstrukcji betonowych. Definicje, wymagania, sterowanie jakością i ocena zgodności. Część 2: Systemy ochrony powierzchniowej betonu
[19] – PN-EN 1504-3:2006 Wyroby i systemy do ochrony i napraw konstrukcji betonowych — Definicje, wymagania, sterowanie jakością i ocena zgodności — Część 3: Naprawy konstrukcyjne i niekonstrukcyjne
[20] – PN-EN 1504-4:2006 Wyroby i systemy do ochrony i napraw konstrukcji betonowych — Definicje, wymagania, sterowanie jakością i ocena zgodności — Część 4: Łączenie konstrukcyjne
[21] – PN-EN 1504-5:2006 Wyroby i systemy do ochrony i napraw konstrukcji betonowych — Definicje, wymagania, sterowanie jakością i ocena zgodności — Część 5: Iniekcja betonu
[22] – PN-EN 1504-6:2006 (U) Wyroby i systemy do ochrony i napraw konstrukcji betonowych — Definicje, wymagania, sterowanie jakością i ocena zgodności — Część 6: Kotwienie stalowych prętów zbrojeniowych
[23] PN-EN 1504-7:2006 (U) Wyroby i systemy do ochrony i napraw konstrukcji betonowych — Definicje, wymagania, sterowanie jakością i ocena zgodności — Część 7: Zabezpieczenie korozyjne zbrojenia
[24] PN-EN 1504-8:2006 Wyroby i systemy do ochrony i napraw konstrukcji betonowych — Definicje, wymagania, sterowanie jakością i ocena zgodności — Część 8: Sterowanie jakością i ocena zgodności
[25] – PN-EN 1504-10:2005 Wyroby i systemy do ochrony i napraw konstrukcji betonowych — Definicje, wymagania, sterowanie jakością i ocena zgodności — Część 10: Stosowanie wyrobów i systemów na placu budowy oraz sterowanie jakością prac
WARSTWY – DACHY i ŚCIANY 4/2007
Dobry tekst